La promesa de Cegid
¿Por qué elegir Cegid Valuekeep?
Gestión de activos
Gestión de mantenimiento
Gestión de inventario
Gestión de órdenes de trabajo y solicitudes
Seguimiento y registro del trabajo
API REST para conectar con otros sistemas

Gestión de activos
Maximiza el ciclo de vida de todos tus equipos
Gestiona los activos en tiempo real. Obtén una visibilidad 360º sobre el estado de tus activos, su rendimiento y ubicación. Vigila el tiempo de inactividad de tus equipamientos y logra reducirlo en un 93%. Además, controla todos los recursos humanos, incluidas las subcontratas.
SOLICITA UNA DEMO
Gestión de mantenimiento
Gestiona de forma más sencilla y eficaz
Programa de manera sencilla los planes de mantenimiento preventivo y todo el trabajo programado como revisiones, tareas y planes. Aumenta la eficacia de tus tareas de mantenimiento, simplifica toda la gestión, automatiza flujos de trabajo y haz que el trabajo fluya.
SOLICITA UNA DEMO
Gestión de inventario
Ten siempre disponible lo que necesitas
Evita que se agote el stock en el peor momento. Controla las entradas y salidas de todas las piezas. Igualmente, obtén todos los costes de los activos, incluyendo mano de obra y piezas.
SOLICITA UNA DEMO
Gestión de órdenes de trabajo y solicitudes
Haz que el trabajo fluya sin interrupciones
Gestiona las tareas de mantenimiento preventivo de forma sencilla y eficaz para que el trabajo fluya. Todos pueden acceder a la información desde cualquier lugar a través de la app de Cegid Valuekeep e igualmente, los colaboradores pueden gestionar y seguir fácilmente sus solicitudes de mantenimiento.
SOLICITA UNA DEMO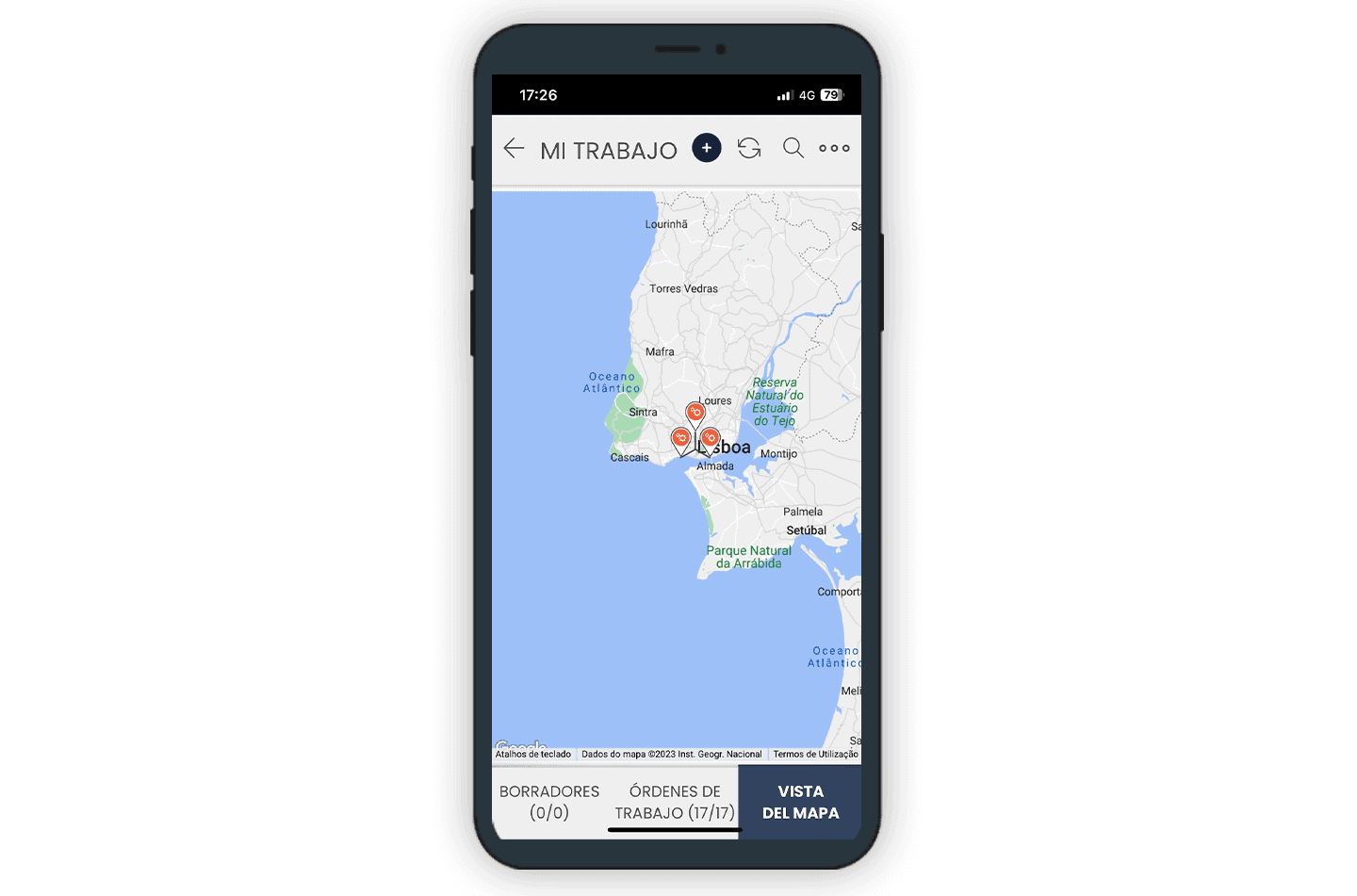
Seguimiento y registro del trabajo
En tiempo real y desde cualquier lugar
Cegid Valuekeep es una solución móvil, en la nube. Puedes controlar las operaciones de mantenimiento en tiempo real, desde cualquier lugar en unos clics. Incluyendo tasas de finalización, costes, etc. Los técnicos podrán acceder a los partes, añadir imágenes, vídeos y registrar y enviar toda la información.
SOLICITA UNA DEMO
API REST para conectar con otros sistemas
Conecta con tu sistema de monitorización o tu ERP
Integra Cegid Valuekeep con cualquier sistema ERP, SCADA, entre otros, a través de una WebAPI. Conecta a las personas, máquinas, procesos, datos y crea OTs desde otros sistemas.
SOLICITA UNA DEMOElige el plan que más se adapte a tu negocio
* usuario/mes. Se aplican condiciones especiales en el caso de suscripciones con múltiples usuarios.
Descubre másCegid te guía
Encuentra nuestro asesoramiento experto para sacar todo el valor a tu negocio.
Accede a nuestros recursosCompleta tu solución Cegid Valuekeep
Cegid Gestiona3w
Gestiona de forma sencilla y en tiempo real trabajos de mantenimiento preventivo, correctivo de cualquier equipo que necesite mantenimiento
- Toda la información accesible desde un único punto
- Planifica para evitar paradas imprevistas y costes
- Controla todas las operaciones en tiempo real
- La IA te ayuda a tomar mejores decisiones